Unlocking Circular Supply Chains in Rare Earth Mine Tailings
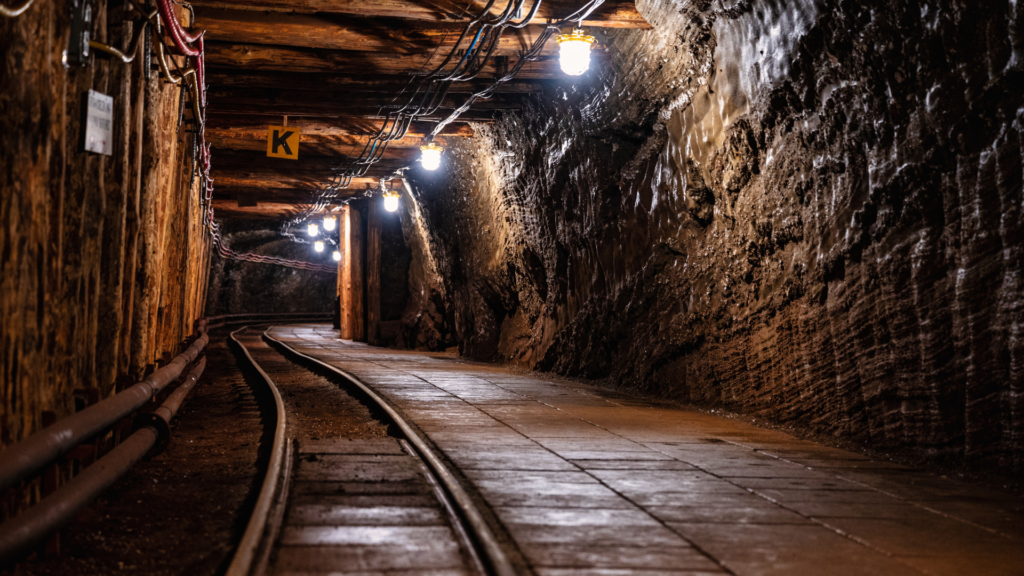
Welcome fellow enthusiasts of the circular economy in rare earth mine tailings supply chain! Are you ready to take a fascinating journey into the world of secondary extraction from mine waste? There’s no denying the criticality of these elements, also known as Rare Earth Elements (REEs), in our high-tech modern world. In this riveting piece, we’ll embark on an exploration of the magic that happens behind the scenes of this innovative industry. Don’t worry, we’ll break down the scientific jargon into bite-sized, 5th-grade comprehensible pieces⏤mining the depths of everything from advanced REE separation techniques to economic and environmental impacts of different recycling methods. Hold on to your hard hats, because this exciting journey towards a sustainable future backed by creative circularity in the REE supply chain starts now!
V. Novel Technologies for REE Separation
When it comes to “Creating circularity in rare earth mine tailings supply chain–Exploring secondary extraction from mine waste,” the race is on for finding the most effective ways to extract and reuse those precious REEs. And the exciting field of novel technologies for REE separation is leading the way.
Advanced Physical Separation Techniques
These technologies use physical properties like magnetism and density to separate out the REEs from the materials they’re mixed in with. They’re a bit like super-powered sieves! Let’s take a look at a few of them:
Magnetic Separation
Imagine a giant magnet pulling out all the bits of iron from a pile of rubble. Now scale that down to microscopic levels and you’ve got magnetic separation. This nifty technique makes short work of sorting iron-based REEs like neodymium. Not bad for a day’s work!
Density Separation
Next, meet density separation. This heavyweight champ uses the different densities of materials to sort out REEs. It’s like panning for gold, but instead of nuggets, we’re after rare earth elements!
Froth Flotation
Finally, there’s froth flotation. With a bit of water and some clever chemicals, REEs group together and float to the surface. One quick scoop later and voila! Freshly caught, ready to be used again. Now, who needs fishing when you’ve got froth flotation?
Chemical Leaching Innovations
While physical separation techniques are great, we also have some chemical tricks up our sleeves. Prepare to dive into the world of chemical leaching innovations:
Ionic Liquids
These aren’t your regular liquids. Ionic liquids have a special superpower – they can dissolve almost anything, REEs included. It’s like having a bottle of universal solvent in your hand. Only safer!
Deep Eutectic Solvents
Up next are deep eutectic solvents. It’s a fancy name, but all you need to know is this: they’re great at extracting REEs without causing harm to our dear Mother Nature. Now that’s our kind of chemical!
Bioleaching with Microorganisms
What if I told you that simple microorganisms can help us in our REE quest? Yup, it’s true! These tiny little workers, like bacteria and fungi, break down the materials, making it easier for us to get the REEs. Just another reason to appreciate the little things in life!
Supercritical Fluid Extraction
Next up is supercritical fluid extraction. This high-tech process uses supercritical fluids (think something between a liquid and a gas) to extract REEs. It’s efficient, it’s clean, and it’s changing the game in REE recovery.
Membrane-Based Separation Processes
Last but not least, we’ve got membrane-based separation processes. This method uses thin sheets (or membranes) with tiny holes to sift out REEs. It’s a bit like making coffee, only instead of a fresh cup of joe, you’re left with pure, ready-to-use REEs.
Stay tuned as we explore more star players in the quest to create circularity in the rare earth mine tailings supply chain!
VI. Reprocessing and Purification of REEs
Creating circularity in the rare earth mine tailings supply chain means making the most out of every grab, dust, and ounce of those valuable REEs – Rare Earth Elements. And a big part of that involves the reprocessing and purification steps.
Solvent Extraction and Ion Exchange
Before your mind starts spinning thinking about what solvent extraction and ion exchange could possibly mean, let me paint a simple picture for you. Imagine you’re sipping lemonade on a hot day. The water in your glass is pulling the sweet and sour flavors out of the sugar and lemon. In a way, you’re performing a simple type of solvent extraction in your kitchen.
But with REEs, everything is more complex. Instead of water, we are using specially designed chemical solutions. These solutions have the knack of pulling out the REEs, leaving the rest of the unwanted minerals behind.
Then, we use ion exchange to purify the REEs further. Just as a beekeeper uses a sieve to separate honey from beeswax, ion exchange uses ions to sift out impurities from the REEs.
Electrochemical Recovery and Refining
This section might sound like rocket science, but essentially, electrochemical recovery and refining is just the use of electricity to get those sparkly REEs. Basically, it’s a bit like a magic trick where you use electric current and a good magician — in this case: an electrolyte solution — to extract and refine the REEs. The beauty of this process is its precision: you get to “call out” which REEs you want to extract and refine!
Precipitation and Crystallization Techniques
You remember how snowflakes form in the cold winter air? Well, precipitation and crystallization of REEs are very similar. We change the conditions of our solutions to make those REEs ‘snow out’ or crystallize. When REEs decide they no longer want to be part of the solution, they form their own solid particles which are easier to collect.
Advanced Techniques for High Purity
High-Performance Liquid Chromatography (HPLC)
When we need to bring out the big guns, we use high-performance liquid chromatography, commonly known as HPLC. Picture a marathon, where each runner (or in our case, molecule) races at a different speed. HPLC is the finish line where we can separate each runner based on when they finish the race. It gives us high precision in separating and isolating each REE molecule.
Capillary Electrophoresis
Last but not least, we have capillary electrophoresis. It’s like a tiny obstacle course for those REEs. We apply an electric field, and each REE, based on its size and charge, wiggles through differently. This sophisticated ‘wiggle-race’ is a cool technique scientists use to identify and separate REEs.
The purification and reprocessing steps are like a special REE festival. The these techniques are the organizers, ensuring that each valuable REE gets their spotlight while removing all the undesired elements that have crashed the party. By mastering these processes, we can make our production more sustainable, cost-effective, and environmentally sound in creating circularity in the rare earth mine tailings supply chain.
VII. Case Studies and Best Practices
In the messed up and tangled world of e-waste lies a gem – Rare Earth Elements (REEs). Yup, you heard me right! Not your everyday food waste or plastic waste, but e-waste is the star. And the crazy-have-to-rub-your-eyes part? You can actually dredge out REEs from this mess. Let’s dive into some super inspiring examples and spruce up your knowledge.
Successful REE Recovery from E-Waste
Have you ever wondered where your old laptops and cellphones end up? Dumpster? Nope! Some daredevil companies have taken the task to extract REEs from this seemingly useless e-waste. You’d be awestruck to know a company by the name of Umicore – these folks are doing unbelievable things!
Starting from Belgium, Umicore has now become an international juggernaut in mining and recycling. They have found a way to treat complex waste like laptops, phones, and other electronic gadgets. How they do it is a trade secret, but guess what, it works! Umicore is successfully giving a second life to these rare metals. Isn’t that just mind-blowing!
Economic and Environmental Impact Analysis
Hang on, before you ask me about the economics of this all, let’s get some facts straight. Mining REEs is expensive and harms the environment big time. But when it comes to getting them from e-waste, it’s like hitting two birds with one stone.
First, you are recovering something invaluable from waste. Second, you are saving the environment by reducing new mining. Now, I don’t have an MBA, but I’d say saving the environment and making money sounds like a darn good deal!
Designing Circular Supply Chains
Now let me tell you about something that makes my heart skip a beat – circular supply chains! Imagine a world where nothing goes to waste. Every electronic item that has fulfilled its destiny comes back in style. Sound like a sci-fi flick? Well, not anymore!
A circular supply chain is the secret sauce that makes this dream a reality. Companies are designing electronic products that can easily be dismantled, reused, and recycled. So, instead of ending in a landfill, these gadgets are reborn in a new avatar, ready to serve us again! Now, isn’t that a fairy tale you’d love to be a part of?
In essence, folks, creating circularity in the supply chain of REEs, especially through the recovery of electronic wastes, isn’t just an imaginative concept anymore. It’s real, happening, and spreading like wildfire! And guess what? It’s saving our dear old earth while doing so.
VIII. Circular Economy Model
In our journey towards sustainable practices, a circular economy model stands as a pinnacle. An economy where we keep resources in use for as long as possible, extract the maximum value from them whilst in use, then recover and regenerate products and materials at the end of each service life.
Design for Disassembly and Recycling
One crucial step to realize circularity in the supply chain of Rare Earth Elements (REE) is to design our electronic products for disassembly and recycling from the get-go. It’s similar to crafting a jigsaw puzzle, designing every piece knowing well that someday it’ll need to be taken apart and put back together again but in a different form. It not only focuses on creating products that can be easily divided into their constituents, but also aims to ensure that these components can be recycled efficiently. The whole idea is to get the most out of our resources and minimize waste.
Extended Producer Responsibility Programs
Now, let’s turn our attention to Extended Producer Responsibility (EPR) programs. These programs push an exciting idea: the responsibility for the disposal of products, especially e-waste, should lie with the original producers. The logic is simple and powerful: you made it, you take care of it. This helps ensure that producers make their products as easy to recycle as possible, as it’s in their best interest to minimize waste. EPR programs stand as a much-needed nudge in the direction of a circular economy.
Urban Mining and E-Waste Collection
Urban mining may sound like a new concept, but it’s quite simple – instead of digging deep holes in the Earth to extract minerals, let’s extract them from our very own cities, in what we often discard as waste! With the vast amount of e-waste we produce, urban mining is no less than a goldmine. It’s about time we leverage these practices to collect discarded electronic products, ensuring our cities don’t turn into electronic graveyards.
Marketplace Development for Recycled REEs
Imagine having a marketplace dedicated to recycled REEs! That’s right; just like we have stock markets, there can be a market where companies can buy and sell recycled REEs. It’s a win-win for everybody. Producers can make money from their waste, companies get a steady supply of REEs, and we protect the environment by reducing unnecessary mining activities.
To sum it up, a circular economy model is perfectly suited to handle our REE needs. Maximizing the lifecycle of our products, taking responsibility for the after-effects and turning our cities into assets instead of liabilities, all whilst enabling a marketplace for efficient reuse. It sounds like an ambition worth pursuing, doesn’t it?
IX. Policy and Regulatory Framework
The laws and regulations governing electronic waste, specifically the extraction of rare earth elements, play a significant role in achieving a circular mining supply chain.
Existing E-Waste Regulations
From the United States to Singapore, government bodies around the globe have established guidelines and rules ensuring safe and responsible e-waste disposal, and more increasingly, recycling. For example, Europe’s Waste Electrical and Electronic Equipment (WEEE) Directive promotes the collection and recycling of e-waste. E-Stewards and R2 Standards in the United States, on the other hand, offer certification for electronics recyclers demonstrating responsible recycling practices.
Such rules require any business dealing with electronic goods, from manufacturers to recycling companies, to adhere to strict procedures in the handling of e-waste. These procedures often involve proper disposal methods, the storage and transportation of e-waste, and acceptable treatment processes. However, these existing regulations, though important for safe e-waste management, fall short of actively promoting the extraction of value from such waste.
Recommendations for Improvement
The current challenge lies in transforming e-waste from a problem into an opportunity. As such, regulations should incentivize the recovery of REEs from electronic waste. Imposing landfill bans on electronics could be a powerful trigger, encouraging the reuse and recycling of e-waste. A systematic certification system for businesses recovering REEs from e-waste would also help in ensuring ethical and environmental standards are met. Similarly, education and awareness programs should be part of regulatory strategies to change consumer behavior towards electronic disposal and recycling.
Another critical aspect is creating a level playing field. For that, government support can be instrumental. For instance, taking steps to reduce the cost associated with recycling processes, like tax benefits or subsidies, can encourage more businesses to recycle e-waste.
International Collaboration
Given the global nature of the e-waste problem and the trade in electronic products, international collaboration is key to effective e-waste management and REE recovery. Transnational bodies like the United Nations could play a vital role in harmonizing e-waste regulations across borders.
Moreover, joint research initiatives and knowledge sharing among nations could lead to innovative and sustainable REE recovery methods. A coordinated international approach can also prevent illegal e-waste dumping in countries with weak environmental policies, thus ensuring a globally responsible approach towards e-waste management.
In a nutshell, policy plays an essential role in our path towards a circular rare earth mining supply chain. By strengthening current regulations, adopting proactive measures, and fostering global cooperation, we can turn the tide on e-waste, making the most of this rich resource.
X. Economic and Environmental Impact Assessment
Cost-Benefit Analysis
Let’s dive right into the nuts and bolts of the matter. When we talk about the Cost-Benefit Analysis, we’re seeing whether the juice is worth the squeeze. Are we getting a bang for our buck by extracting rare earth elements (REEs) from waste?
The answer is a resounding YES! First, we’re saving some serious dollars on mining costs. But that’s just the tip of the iceberg. We’re also raking in the environmental benefits, like reduced land degradation, fewer chances of health problems in local communities, no to mention the reduction in CO2 emissions. When we weigh the benefits against the costs, we’re coming out on top.
Life Cycle Assessment
Switching gears to the Life Cycle Assessment, this is a whole other ball game. Here, we’ve got our eyes on the prize all the way from ‘cradle to grave.’ Sounds morbid, I know, but it’s all about following the journey of electronic products from their creation to their disposal or recycling.
What’s the upshot? By recycling REEs from e-waste, we’re not only giving a second life to valuable elements but also reducing the environmental burden at every stage of the product’s life cycle. It’s a win-win situation, folks!
Mining vs. Recycling Impacts
Last but definitely not least, we’ve got the Mining vs. Recycling Impacts to ponder. Picture this. On one hand, you have mining ‐ ripping up the earth, tears in Mother Nature’s eyes. On the other hand, you got recycling ‐ harmonious, balanced, a real crowd-pleaser.
So, when you stack mining against recycling, it’s clear as day that the scale’s tipping in favor of recycling. Reduced greenhouse gas emissions, less water wasted, minimal soil and water pollution – the list just keeps going on.
In the grand perspective of creating circularity in the rare earth mine tailings supply chain, these economic and environmental assessments illuminate the path toward a sustainable, brighter future. So, folks, let’s keep the momentum going!
XI. Future Directions and Research Needs
What does tomorrow hold for the world of Rare Earth Elements (REEs)? Well, I’m glad you asked! This section is all about the horizon of innovation for REEs. We are heading towards new territories marked by efficiency, integration of technology, and exploration. Gird up your loins, my friends. Exciting times are ahead.
More Efficient Technology Development
When it comes to REE extraction, the name of the game is efficiency. We’re talking faster, cleaner, and less wasteful tactics. Look, it’s simple. The more REEs we can extract from waste, the better it is for everyone. Less waste, more valuable material. It’s a win-win situation!
Innovations are needed that focus not just on obtaining these important elements from e-waste but doing it in a way that is economical and ecological. One exciting frontier is the development of more efficient REE separation and reprocessing technologies. Imagine a future where we can extract virtually all the REEs from our discards!
AI and Machine Learning Integration
Now let’s talk about smart tech. Artificial intelligence and machine learning? Yes, please! These aren’t just futuristic terms making waves in the corridors of Silicon Valley. They have very real implications for the REE industry.
Think about it. By integrating AI and machine learning, we could revolutionize the way e-waste gets sorted and recycled. Picture an assembly line with smart machines, expertly sorting through tons of e-waste to recover these crucial elements. Not only would this increase recovery rates, but it would also significantly decrease the need for manual labor. That’s impressive, right?
Alternative Materials Exploration
Last, but certainly not least, let’s talk about exploration. No, not the kind with pirates and treasure maps, but exploration of alternative materials for microchips. Why, you ask? Well, reducing our reliance on REEs can ease the pressure on supply chains and make it easier to recoup and recycle these valuable resources.
In simpler terms, if we can find other materials that serve the same function as REEs in our electronics, we’ve got ourselves a much more sustainable system. It’s like finding a new route home that cuts your travel time in half. It’s all about making the journey smoother!
And that’s the future, my friends. One marked by efficiency, smart technology, and exploratory innovation. It’s going to be a wild ride! Let’s gear up and face this brave new world head-on.
XII. Conclusion
Folks, it might seem like we just took a whirlwind tour through the exciting world of circularity in the rare earth mine tailings supply chain, but in reality, we’ve just scratched the surface. Let’s pause to recap why this journey is so crucial.
Importance of Circularity
Creating a circular supply chain for electronic waste is more than merely a good idea—it’s a necessity. Every year, tons of valuable rare earth elements (REEs) are lost, dumped into landfills when their host gadgets bite the dust. This is as good as throwing money in the trash and lighting a match to it! By closing the loop, we not only salvage these valuable metals but also significantly reduce the strain on our limited natural resources.
Potential of Novel Technologies
Now let’s talk about the kindling that can ignite this circular revolution – novel technologies. We’ve explored a slew of them, from the innovative physical separation techniques like magnetic and density separation, to groundbreaking chemical solutions, and even bioleaching with hardworking microorganisms. Each one of these transformative technologies holds the potential to pry out precious REEs from previously seen-as-worthless e-waste. And all while keeping the environmental impact as low as possible.
Call for Collaboration
Finally, let’s do the classic Halbert and hit you with a challenge. We need everyone on board to make the shift towards a circular economy happen. It’s not just on the tech wizards to come up with snazzy separation techniques or nifty AI solutions. We need policymakers to implement strong, effective e-waste regulations. We need businesses to take responsibility for the full lifecycle of their products. And, yes, we need you, the consumers, to support initiatives aimed at raising recycling rates and holding manufacturers accountable.
In conclusion, our journey towards achieving circularity in the rare earth mine tailings supply chain has only just begun, and there’s a lot of ground to cover yet. But, every step we take in this direction gets us closer to a more sustainable, more prosperous future. Are you on board?