Achieve Circularity by Turning Auto Waste into a Resource by Recycling Car Plastics
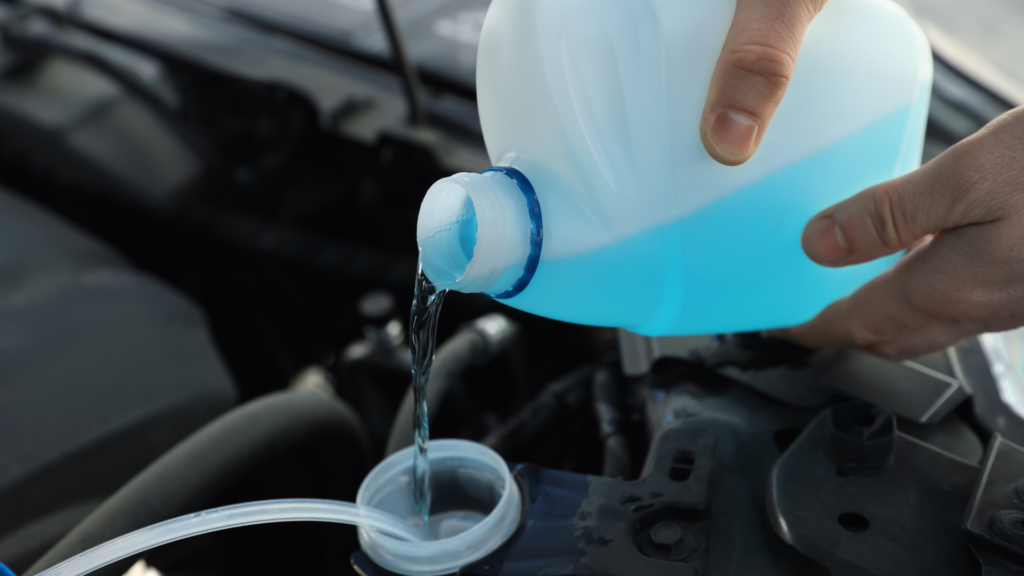
Let’s embark on an exciting journey to revamp our automotive waste management, where dashboards, bumpers, and under-hood components, commonly destined for the landfill, get a complete makeover! This unmissable venture aims to supercharge transformation in automotive plastic waste, unfurling innovative closed-loop systems for reclaiming every bit of PP, ABS, PC, TPO, PU, PE and other composite materials. We’re going to bring design, technology, and regulation together, turning challenges into lucrative opportunities—because recycling automotive plastic is about more than just “doing good.” It’s about crafting a sustainable future for our industry, creating jobs, conserving resources, and even tackling some of our toughest environmental challenges. So, hop in, buckle up, and let’s drive towards an era where nothing goes to waste!
Understanding Automotive Plastic Waste
When it comes to automotive plastic waste, there’s a truck-load of stuff to wade through. But hold onto your headrests, folks; we’re about to hit full throttle into the world of automobile plastics!
Types of Plastics in Automobiles
Polypropylene (PP)
Starting up the engine with our first plastic, Polypropylene (PP). PP is like the trusty ol’ pickup truck in the world of plastics – sturdy, reliable, and used in just about everything! From dashboards to seats and even under the hood, PP is a key player in the auto game.
Acrylonitrile Butadiene Styrene (ABS)
Next up, we’ve got Acrylonitrile Butadiene Styrene or ABS – a tough guy used in hard interior parts. Fasten your seatbelts, folks; ABS is resilient and brings the brawn to stand up to some considerable wear and tear.
Polycarbonate (PC)
Zooming into the scene is Polycarbonate (PC). You’ll find PC in headlamp lenses and other exterior parts. Pretty important stuff, right?
Thermoplastic Olefins (TPO)
TPO, short for Thermoplastic Olefins, is used in making sturdy bumpers and liner carpets. Trust me, you don’t want to skimp on these!
Polyurethane (PU)
Finally, we’ve got Polyurethane (PU). It’s flexible and durable – perfect for foam seats and the insulation material under that glossy car hood!
Environmental Impact
Now, shifting gears to discuss the impact of these plastics on our environment.
Waste in Landfills
Did you know, most of our old auto plastics end up as waste in landfills? That’s a dirty wasteland of precious resources just sitting there! And it’s not just taking up space; it’s also releasing harmful chemicals into the soil and water. Not a good look for Mother Earth, huh?
Resource Depletion
It’s not just about waste either; it’s about the raw materials used to create this stuff in the first place. We’re drilling oil and gas to create them, often in sensitive habitats. That’s a lot of damage for something we just ultimately toss away!
So there you have it, folks! That’s the low-down on the types of plastics in your cars and their environmental impact. They’ve got the potential to pose some serious challenges, but remember, they also offer us opportunities to improve, innovate, and create a sustainable future. So, let’s get that engine revving and hit the road on the journey to circularity in automotive plastic waste!
Design for Circularity in Automotive Plastics
Creating circularity in automotive plastic waste requires a fresh look at how we design car parts. It’s not just about recyclability, but also about seeing the big picture from the very beginning.
Material Selection
The first decision in this journey is picking the right materials.
Choosing Recyclable Materials
For starters, we ought to opt for plastics that lend themselves well to recycling. This includes the likes of polypropylene (PP) or acrylonitrile butadiene styrene (ABS). By designing parts with recyclable materials, we’re paving the way for easier recycling down the line.
A tip for those Googling on how to choose recyclable materials? Pay attention to the Resin Identification Codes (RIC), numbers you’ll find inside the chasing arrows on plastics. They can help identify the type of plastic, and hence, its recyclability.
Durability Considerations
On one hand, using recyclable materials is big thumbs up. On the other, these materials need to be tough enough to withstand use.
Automobiles aren’t exactly gentle on their parts. They need to endure diverse temperatures, forces, and chemicals. Plastics such as polycarbonate (PC) and thermoplastic olefins (TPO) might be top candidates here.
Modular Design
The second pillar to focus on in this circularity journey is creating a modular design.
Easier Disassembly
In essence, this represents designing in a way that makes taking the car apart simpler. Imagine being able to remove a dashboard or a bumper with ease when its life cycle has ended. That’s the kind of disposal-friendly thinking we need.
Why does that matter? Well, easier disassembly means easier removal of materials for recycling. And that’s our end game.
Standardization Benefits
Including a standardized design offers sweet bonuses, too. It can make sorting and recycling processes more efficient since you’re dealing with identical parts. Standardized plastic components could also improve quality control, reducing the need for wasteful rejections.
Just imagine this – a world where automotive plastics get a second, third, or even fourth life! Not only would this incredibly reduce environmental harm, but also reinvent the economies around car manufacturing and waste management. Now, that’s a GPS route worth following.
Advanced Recycling Technologies
In today’s rapidly advancing world, traditional recycling methods are not the only tools in our belt to tackle the problem of automotive plastic waste. More sophisticated techniques have been developed to enhance the circularity of automotive plastics and they can be broadly categorized into two big subgroups: ‘Automated Sorting’ and ‘Chemical Recycling’.
Automated Sorting
The first step towards recycling automotive plastics effectively is sorting them right. This may seem like a simple task, but the variety of materials used in constructing a single vehicle makes it way more complex than it sounds. Let’s dive into two leading technology-driven sorting methods.
AI and Robotics
Artificial Intelligence (AI) and Robotics have a huge role to play in the automatic sorting of automotive plastic waste. Now, you may imagine, Terminator-like robots sorting plastics, although not totally off, it’s less dramatic. Here, robots equipped with AI software can recognize and distinguish between different types of plastics based on their properties. Cool right? This is a massive game-changer because it boosts the efficiency of the sorting process while reducing the amount of plastic that mistakenly ends up in the wrong pile.
Near-Infrared (NIR) Sorting
Another sci-fi sounding method is Near-Infrared (NIR) Sorting. This clever system uses light, specifically near-infrared light, to identify different types of plastics. Just like people, plastics too, absorb and reflect light differently. And NIR technology exploits this property to efficiently and accurately sort plastics on the go.
Chemical Recycling
Chemical recycling is the next big step in the recycling process and offers solutions to recycling plastics that are harder, or in some cases, impossible to recycle through traditional means.
Understanding Pyrolysis
Sounds something out of a Sci-Fi film, doesn’t it? Well, its science alright, but quite real. Pyrolysis is a chemical recycling method that uses high heat in a no-oxygen environment to break down plastics into smaller molecules. These can be further refined and used as base materials for new plastic products, offering a way not just to recycle but to upcycle!
Solvent-Based Methods
The last method on our list is solvent-based recycling which dissolves the plastic in a special solvent. The solution is then filtered, purified, and the solvent is evaporated, leaving behind the stripped-down plastic material, ready to become something new!
Wrapping it up, advanced recycling technologies such as AI and robotics for automated sorting, and chemical recycling techniques like pyrolysis and solvent-based methods offer exciting pathways to improve the circularity of automotive plastic waste. With these technologies, we can aim for a future where landfill waste is significantly reduced, opening the doors for lower emissions and a healthier planet.
Recycling Specific Automotive Components
When it comes to the circularity of automotive plastic waste, specific components of the car demand a particular examination – let’s drive into this topic.
Recycling Dashboards
Dashboards are one crucial element in a car’s interiors, consisting of numerous types of plastic materials.
ABS and PC Recovery
To start with, the ABS (Acrylonitrile Butadiene Styrene) and PC (Polycarbonate) found abundantly in dashboards get a new lease on life through advanced recycling processes. This involves separating these plastic types from mixed waste streams and converting them back into high-quality ABS and PC suitable for new manufacturing. Now that’s creating a loop – your old dashboard turning into the raw material for a new one!
Challenges with Integrated Components
However, recovering ABS and PC from dashboards is a bit like trying to untangle spaghetti! It’s tricky because dashboards often contain integrated components – like embedded electronics and mixed material parts, leading to contamination of recovered plastics. Yet, nothing is impossible. Modern technology, like precision dismantling and advanced sorting, is showing a ray of hope.
Recycling Bumpers
Now moving outside, the bumper of your car has some hard-core plastics on it.
Processing PP and TPO
Bumpers are typically made from robust and resilient plastic types like PP (Polypropylene) and TPO (Thermoplastic Olefins). The good news is PP and TPO are good buddies for recycling. So, with innovations in advanced recycling, your car’s old bumper could bounce back as a fresh one.
Dealing with Coatings and Reinforcements
Hold on, there’s a speed bump! Bumpers often come with coatings and reinforcements – think of paint layers and metal frames. These extras play spoil-sport in the recycling game, creating hurdles in clean recovery of PP and TPO. Yet, removing these nuisances with advanced mechanical processes and chemical treatments can put you back on the smooth road to circularity.
Recycling Under-Hood Components
The engine hood hides a hotchpotch of heat-resistant plastics.
Heat-Resistant Plastics Options
Components located under the hood must withstand high heat and harsh operating conditions. High-performance plastics like PF (Phenol-Formaldehyde), PPS (Polyphenylene Sulphide), and PEEK (Polyether Ether Ketone) serve this purpose. Although these plastics are not frequently recycled, recent advancements in thermal decomposition and chemical recycling promise a brighter future for these heat-lovers.
Managing Oils and Chemicals
Under-hood parts, laden with oil and chemicals during the car’s life, need careful handling. Specialized cleaning and treatment processes ensure these contaminants don’t taint the recycling stream.
By tackling each component’s specific recycling challenges head-on, we pave the road towards creating circularity in automotive plastic waste. This is just one small gear in our giant circulatory engine. And the journey continues…
Strategies for OEM and Supply Chain Management
In our journey towards a circular economy in the automotive plastic space, the heroes of the hour are the Original Equipment Manufacturers (OEMs) and the supply chain management teams. This, my friends, is where the magic needs to happen!
Implementing Industry Standards
Role of Extended Producer Responsibility (EPR)
The car manufacturers aren’t just making fancy toys for us to ride around in. They play a huge part in dealing with the whole life-cycle of their products, including the end-of-life of their plastic parts. That’s called Extended Producer Responsibility (EPR).
In a nutshell, EPR is like a parent taking full responsibility for their children, even when they mess up and leave their toys all over the place. It involves car manufacturers stepping up and saying, ‘Hey, we made these plastic parts, so we’ll make sure they don’t end up ruining our planet!’ Quite nifty, isn’t it?
Reverse Logistics Processes
Okay, now let’s wrap our heads around the notion of reverse logistics. Think of it as doing the Hokey Pokey dance – you put your right foot in (send a product out to the customer), you take your right foot out (get the product back when it’s no longer useful). In the world of recycling, this ‘taking out’ is all about gathering used products from the customer, like a car dashboard, and getting it back to where it can be recycled or disposed of safely.
Building Partnerships
Collaborating with Recyclers
Now, this is where the party begins in the recycling world! Car manufacturers and supply chains can’t do this dance alone. They need to hold hands with the recycling guys, the ultimate movers and shakers in our story. Recyclers are the ones who take the old dashboards, bumpers, and other parts and transform them into useful raw materials once again. It’s all about teamwork!
Stakeholder Engagement Strategies
All the key players from manufacturers, suppliers, and recyclers need to join the dance. So how do we get them all moving to the same beat? Stakeholder engagement, my friends! It’s like setting up a big party and making sure everyone feels invited. Everyone’s ideas, resources, and roles are important in keeping plastic waste out of the landfills and in the circular economy where they belong!
So there you have it! The exciting world of OEM and supply chain strategies in creating circularity in automotive plastic waste. Tune in next time for more on this fascinating journey!
Consumer and Policy Influence on Circularity
When it comes to creating a “vicious circle” in the recycling of automotive plastics, you and I play an essential role, believe it or not. Interested? Let’s dive in!
Educating Consumers
Benefits of Recycling
So, why recycle, you may ask? Just imagine this; Every bumper, dashboard, or under-hood part you recycle saves a chunk of raw material, conserves energy, and lets Mother Nature breathe easier. Yep, it’s that big a deal! Also, your favorite car manufacturers can reuse these materials, making it a win-win for everyone involved.
Incentives for Participation
I know, you need that little “nudge” to start recycling. Well, some pretty smart people are ahead of you, cooking up incentives to make recycling worth your while. These could be discounts on new parts, or even eco-points that add up to a surprise gift! Curious about what’s on offer? Just ask your car dealer or local recycling center.
Policy and Regulation
We can’t do it all alone, though. We need a little help from our friends in high places.
Regulatory Incentives and Challenges
Governments worldwide are pulling up their socks and enacting regulations to favor recycling. Things like extended producer responsibility (EPR) are making manufacturers responsible for their products, end-to-end. Sounds like a challenge, right? But it’s also an opportunity. With EPR, manufacturers are incentivized to design for recyclability right from the word “go”.
Product Take-Back Schemes
Ever heard of the “Cradle-to-Cradle” concept? It’s pretty cool. It means a product is designed to be recycled into a new product at the end of its life. Governments are encouraging such schemes, where you can return your old car parts, and guess what – get rewarded for doing that!
So folks, be it through self-motivation or with a push from our policies, we have the power to make a change! Let’s create a “vicious circle” of recycling in the automotive industry, shall we?
Leveraging Technology and Innovation
In the race towards a circular automotive industry, technology and innovation are our greatest allies. They bring in a dash of efficiency, accuracy, and adaptability, just what we need to blitz through the plastic waste recycling process.
Technological Advances
Role of AI in Recycling Processes
Artificial Intelligence (AI) technology has been a wonder tool in the recycling process. One might ask, “how can a computer help recycle plastic?” Well, surprisingly, it’s pretty adept at it! AI systems can quickly analyze and sort plastic waste, distinguishing between the many types of plastics found in vehicles. This speedy sorting saves us humans countless hours and energy while increasing the quality and purity of the reclaimed materials. AI is our speedy conductor in the recycling orchestra, ensuring everything keeps playing in perfect harmony.
Blockchain for Tracking Materials
Blockchain, the same technology that powers Bitcoin, has an equally powerful role in our journey toward circularity. This advanced tech helps us to accurately track materials through the supply chain, following every plastic piece from the manufacturer to the recycler and back again. It’s like having a GPS for every bit of plastic, allowing us to ensure nothing gets lost or misplaced and every piece gets another chance at life.
Innovative Manufacturing Practices
Impact of 3D Printing
Our tech exploration doesn’t stop at recycling. It goes a step further into manufacturing. With 3D printing, parts can be manufactured on-demand, reducing production waste. Even more, 3D, when combined with recycled plastics, can spin out completely sustainable parts, fitting perfectly into our circular model. Imagine creating a brand-new dashboard out of an old one, all thanks to the magic of 3D printing!
Digital Passports for Parts
Digital passports might sound like something out of a sci-fi movie, but they’re indeed a part of our technology arsenal. These virtual tickets contain vital information about each component, such as its material composition, its origin, and its recyclability. With these passports, we not only have a better understanding of each component in a vehicle but also a clearer path for recycling or repurposing.
In conclusion, the monumental task of creating circularity in automotive plastic waste management finds surprising allies in burgeoning technologies. From AI-driven sorting to 3D printing parts on-demand, each innovation fuels our journey in transforming mounds of plastic into completely reusable resources. Now that’s one way technology is not only driving our cars but also steering the wheel of sustainable change!
Benefits and Challenges of Circularity
When you glance into the rearview mirror of your car, you might not realize the treasure trove of recyclable material that’s staring back at you. Yet, creating a circular economy for automotive plastic waste is a road filled with fruitful benefits and winding challenges.
Key Benefits
Reducing Waste and Emissions
Let’s talk about making Mother Earth smile by slashing the waste we send to the landfills and the emissions we pump into the air. Giving a second life to the plastics in our cars, notably our dashboards, bumpers, and under-hood components, can dramatically reduce the need for raw materials. Less raw material mining equals less CO2 emissions! Plus, when we recycle, we’re saving valuable items from an eternity in a landfill. Imagine your car’s dashboard coming back as a brand-new one instead of wallowing in a waste heap.
Cost Savings and Job Creation
Dollars and jobs – two things most of us care deeply about. By riding the circular wave, we could be boosting both. Breaking and remaking plastic requires less energy than creating fresh plastic from petroleum. Less energy expense equals cost savings. Plus, the surge in recycling would stimulate job growth in the waste management and recycling industry. So, by promoting plastic circularity, we’re fueling an economic engine that everyone can ride on.
Addressing Challenges
Much like a pothole-laden road, the journey to circularity has its bumps and challenges.
Technical and Logistical Barriers
We’ve got a list of technical brain-busters to conquer. For instance, cars contain many different types of plastic, often glued or welded together in complex designs. Sorting and separating these materials takes smarts and effort. Likewise, we must deal with the effects of heat and chemical exposure on under-hood plastics. And don’t get us started on the logistical challenges of collecting, sorting, and transporting these materials for recycling.
Navigating Regulatory Hurdles
Rules and regulations also put up roadblocks on our circular journey. Without robust policy support or incentives to encourage recycling, some manufacturers and consumers might opt for the easy route and continue with a one-way trip to the landfill.
To sum it up, the road to a fully circular automotive plastic economy might not be an easy one, but boy, is it a road worth traveling! Remember, it’s not just about what we’re saving; it’s also about what we’re creating – a sustainable, greener future for generations to come.
The Future of Automotive Plastic Circularity
Looking ahead, the future of automotive plastic circularity is as bright as a polished bumper on a hot rod. It’s not just about recycling old favorites anymore – it’s about maximising new materials and innovative recycling practices.
Innovative Material Developments
explore these two hot topics: bioplastics and advanced composites and hybrids.
Potential of Bioplastics
First up, let’s rap about bioplastics! Made from renewable resources, bioplastics could drastically reduce our dependence on fossil fuels. The big question is: can we make them tough enough and kind enough to handle life on the road? There’s a bunch of brainy folks out there working on doing just that.
Not only can these green machines potentially be composted at the end of their life, they further add to the circularity by reducing CO2 emissions during their production. Aces!
Advanced Composites and Hybrids
But hang on — it’s not just bioplastics. There are rumblings about advanced composites and hybrid materials. These babies can drive the performance of auto parts without losing those circular brownie points from lighter weight and recyclability.
Emerging Recycling Practices
With new materials on the block, we need new recycling practices to keep the circle spinning.
Localized Recycling Systems
Localized recycling systems are a new trend. Instead of shipping materials across the globe, think local! Break ‘em down and build ‘em up – all in the same place. By keeping it local, we save on transportation and reduce emissions. Plus, we strengthen local economies by creating jobs. It’s a win-win.
On-Demand Manufacturing Innovations
And then there’s on-demand manufacturing. This isn’t an assembly line churning out thousand of widgets. Nope, it’s the total opposite. It is agile, making parts as and when they are needed. Mix in 3D printing and you can go from concept to component in a blink of an eye.
These might sound like ideas for the distant future. But let me tell you, they’re closer than you think! Automotive plastic circularity doesn’t just have a bright future, it’s becoming the future. So, buckle up, folks! The ride is just getting started.
Remember: Creating circularity in automotive plastic waste supply chain – Recycling dashboards, bumpers, and under-hood components isn’t a postscript — it’s a script for our future. Let’s make it happen!