Process Intensification: Transforming Chemical Manufacturing Efficiency
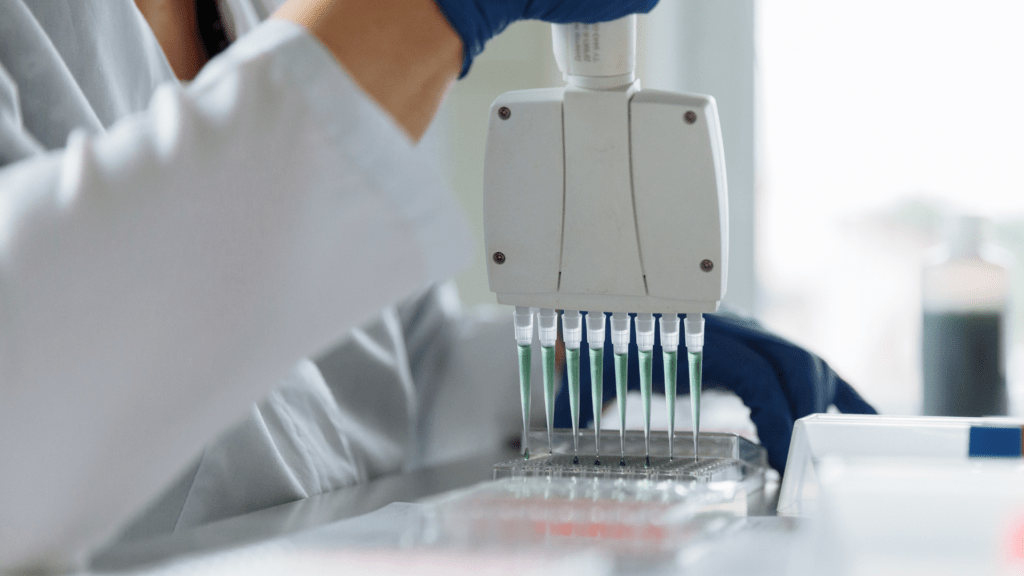
Process Intensification, the magic behind making chemical processes more efficient and compact, is transforming the world of chemical manufacturing! Imagine creating more with less, achieving higher yields while shrinking the size of equipment. This innovation isn’t just about being more efficient—it’s also about being more sustainable and economically viable.
As we dive into optimized chemical manufacturing, we’ll explore the journey from traditional methods to cutting-edge technologies like microreactors and membrane reactors. These advancements are paving the way for greener processes and safer environments. If you’ve ever wondered about how faster reactions and energy savings are achieved, you’re in for a treat! Hold tight as we unravel these fascinating advancements that are revolutionizing industries from pharmaceuticals to water treatment!
The Basics of Process Intensification
Why Process Intensification Matters
Boosting Efficiency and Sustainability
Process intensification is like a superhero for chemical processes. It saves the day by making them more efficient and sustainable. This means we can get bigger results with less waste. It’s like baking a cake with fewer ingredients but still getting the tastiest treat. With process intensification, we use less energy and produce fewer emissions, which is good for our planet. For example, reactive distillation allows certain reactions and separations to happen at the same time, boosting efficiency. So, if you’ve ever wanted to make things faster while being kind to nature, this is how it’s done!
Making Chemical Processes Compact
Ever heard of fitting huge things into tiny spaces? That’s what making chemical processes compact is all about. Imagine shrinking a big factory into the size of a cozy garage while keeping its power and magic. This is possible with microreactors and other compact technologies. They allow us to perform the same tasks in much smaller spaces. This not only saves money but also makes it easier to control the processes. Plus, using smaller tools can lead to faster reactions and better quality. It’s like having a Swiss Army knife that packs loads of functions in a small gadget.
The Story Behind Process Intensification
From Traditional to Innovative Designs
Once upon a time, chemical processes had to grow bigger to produce more. But then, the world of chemistry introduced process intensification. It said, “Let’s make these processes smaller and cleverer!” Instead of building large equipment, the focus shifted to innovative designs that integrate processes and improve transfer rates. This shift from traditional to innovative designs means that we can achieve more with less. So, the tale of process intensification is one of evolution where new technology and ideas team up to redefine what’s possible in chemical engineering.
Rising to Meet Modern Demands
In the modern world, we want things to be fast, efficient, and safe. Process intensification works like a charm in meeting these demands. As industries grow, so do their needs for sustainability and safety. By adopting process intensification, businesses can operate in leaner and cleaner ways. The integration of technologies like membrane reactors means businesses can produce biofuels more efficiently. This method isn’t just about doing things better; it’s about reshaping how we think about manufacturing processes in response to modern challenges.
Key Principles of Process Intensification
Process Intensification. That’s a big phrase, but the idea is simple. It’s like turbocharging a car to make it go faster without making it bigger. When we think of speeding up a chemical reaction, we think of Improving Mass and Heat Transfer. Using just the right tools can make chemicals move and react quicker, almost like magic!
Improving Mass and Heat Transfer
When we say mass and heat transfer, we’re talking about moving things—like heat or chemicals—around in smart and efficient ways. Imagine stirring a pot of soup quickly so it heats evenly.
Using Microchannels and Static Mixers
Microchannels and static mixers are the secret weapons here. Microchannels are like tiny highways for chemicals, letting them zoom around and mix much faster than before. Think of static mixers as small guides that keep everything flowing in just the right direction. They don’t move, but they make sure everything else moves smoothly. By using microchannels and static mixers, we save time and energy, making everything work better and faster!
Integrating Processes for Efficiency
Doing jobs one at a time is slow. Imagine taking separate trips to buy milk, eggs, and bread. But what if you can do it all at once? That’s where integrating processes for efficiency comes in, making everything happen together smoothly.
Reactive Distillation and Membrane Reactors
Reactive distillation combines two jobs — mixing things up and unmixing them later. It’s like baking a cake and slicing it all at once! Membrane reactors are like super-sieves, letting the right stuff through while keeping unwanted stuff out. Both reactive distillation and membrane reactors improve efficiency, reducing time and effort.
Boosting Energy Efficiency
Everyone likes saving energy, right? It’s not just good for our environment but also for our pocketbooks. So, what about making chemical processes more energy-savvy? That’s what boosting energy efficiency is all about.
Including Renewable Energy and Heat Recovery
Using renewable energy—like sunshine and wind—is a big part of energy efficiency. But there’s more! Heat recovery is about capturing heat from a process and using it again. Imagine a sponge soaking up extra water to use again. By including renewable energy and heat recovery, these practices cut waste and boost the overall eco-friendliness of processes!
By understanding these key principles of Process Intensification, we unlock new ways to make chemical processes not just smaller, but also smarter!
Technologies in Process Intensification
In this exciting part of our journey called process intensification, we’re exploring some incredible technologies that make chemical processing more efficient and compact. Let’s dive deep into the world of microreactors, reactive distillation, and membrane reactors. They’re not just fancy words; they’re changing how we think about chemical processes.
Exploring Microreactors
Precision and Speed in Chemical Reactions
Microreactors are like the secret lab behind the curtain where magic happens. They let us control chemical reactions with precision and speed like never before. In these tiny reactors, chemicals dance and mix faster, making reactions happen quicker. It’s like having a race car instead of a bicycle. Microreactors are perfect for making fine chemicals where every drop counts. You get more control, faster transfers, and even higher quality source.
Power of Reactive Distillation
Combining Reactions and Separation for Better Yields
Here comes the superhero technology: reactive distillation. Imagine you’re cooking and instantly cleaning up at the same time. That’s what reactive distillation does by combining chemical reactions and separation in one step. This method helps get better yields using less energy and time. It’s like sending a letter and having it delivered instantly. With reactive distillation, industries can speed up processes and save money at the same time!
Advantages of Membrane Reactors
Improved Selectivity for Clean Energy
Now, let’s talk about membrane reactors. They are the wizards for selecting the right chemicals, making them shine in the green energy world. Membrane reactors help produce hydrogen and biofuels with improved selectivity, meaning they pick out only the best chemicals for the job. This makes energy production cleaner and greener. Membrane reactors work their magic by letting certain chemicals pass while stopping others, making chemical processes both smart and selective and contributing to a cleaner environment source.
In summary, these technologies are like having superheroes saving the day in chemical factories. They’re fast, efficient, and sustainable, making the world of chemistry better and cooler every day!
Applications of Process Intensification
Impact on Chemical Manufacturing
Creating Smaller Plants for Big Results
Process Intensification in the chemical manufacturing sector is like a magic trick—condensing large processes into small packages. Picture this: smaller chemical plants that can do the job of gigantic facilities, but with greater efficiency and less waste. This is not just a wishful dream; it’s a real innovation that caters to the need for less space, lower costs, and higher productivity in today’s operations.
Smaller plants mean reduced capital investment and operational costs. But they don’t stop there. These compact units boast of faster production rates, thereby meeting demands swiftly. Imagine producing chemicals like ammonia and ethylene with just a fraction of the traditional plant size—impressive, right?
Process Intensification in Pharmaceuticals
Achieving Higher Purity Faster
In the world of pharmaceuticals, precision and purity are king. Process Intensification steps into this realm with all it has got. Pharmaceuticals require processes that are not only fast but also that ensure high standards of purity. By introducing intensified processes, drug manufacturing sees a jump in purity with less time spent, which means quicker deliveries to the market.
With intensified processes in place, the production shifts from batch to continuous flow, facilitating consistent and higher quality products. This is a game-changer, ensuring medicines are both safe and effective, reaching patients without delay.
Applications in Energy Sector
Producing Biofuel and Hydrogen Efficiently
Process Intensification shines brightly in the energy sector. With the world striving for cleaner energy, the efficient production of biofuels and hydrogen is critical. Intensified technologies allow these fuels to be produced faster and with greater selectivity. For instance, membrane reactors enhance the process of separating pure hydrogen, making it a preferred source for eco-friendly energy.
The energy sector benefits immensely from reduced emissions and lower carbon footprints. By making processes more efficient and compact, not only is energy conserved, but the efficiency of fuel production is maximized too, heralding a future of sustainable energy solutions.
Find more about advancements in process intensification here.
Overcoming Challenges in Process Intensification
Process Intensification sounds fantastic, but it’s not all smooth sailing. Just like anything new, it comes with its own set of challenges. Let’s dive into some of the hurdles we face in making chemical processes better, safer, and more efficient.
Technical and Economic Challenges
When we’re talking about Process Intensification in chemical manufacturing, there are some big concerns to tackle. It’s about getting from small, clever models to big, real-life plants. And let’s not forget about the money!
Addressing Scale-Up Issues and Investment Barriers
It’s one thing to get a technology to work in a lab. Making it work on a large scale is a whole different story. That’s where scale-up issues come into play. We want to make sure these processes work just as well in big plants as they do in small test setups.
But here’s the catch: scaling up usually needs big money. Investors want to know they’re putting their cash in the right place. They need to see results, not just promises. So, to convince them, we need to show that these new processes are worth it. The processes have to save time, reduce energy, and create better products. You wouldn’t believe how those numbers make investors smile!
Getting over these investment barriers means doing the math and showing how we can save money in the long run. We have to prove it’s not just a fancy idea but a smart investment.
Operational Hurdles
Once we’ve tackled the technical and money parts, we’re not out of the woods yet. Running these new systems smoothly every day is no small feat.
Training and Reliability in New Systems
New systems mean new training. People who run the plants need to know how these intensified processes work, and they need to know it well. Understanding how to handle them, what parts to watch out for, and how to fix problems fast is crucial. It’s not just the machines that need to work well—it’s about the people, too.
Reliability is another big thing. We’re making changes to how things have been done for years. So, folks worry about whether these new systems will hold up and keep delivering quality products. No one wants surprises!
In short, getting everyone up to speed and making sure these new systems are trustworthy takes effort and time. From training programs to regular maintenance checks, every step ensures that the whole system runs like a well-oiled machine.
Dealing with these challenges takes smart planning and teamwork. If we address the concerns head-on, the path to making Process Intensification a reality gets a little bit clearer—and a whole lot exciting.
Design and Optimization Strategies
Design and Optimization Strategies in Process Intensification are like putting together the pieces of a complex puzzle. It’s all about making things fit just right, using the best tools to tweak and refine chemical processes. Let’s dive into how this is done!
Utilizing CFD and Process Simulation
Imagine trying to predict where water will flow if you pour it onto a rocky path. That’s what scientists do when they use CFD and Process Simulation.
Predicting and Improving Flow Patterns
Using CFD, which stands for Computational Fluid Dynamics, lets us imagine how gases and liquids move. It is like having a superpower to see invisible currents! By predicting these flow patterns, we can make sure that everything is moving smoothly. This helps in improving the efficiency of chemical reactions. Learn more about CFD here.
Simulation helps in designing processes that are just right. It’s like doing a test run on a computer before trying it in the real world. By doing this, we not only predict how everything will flow but also find better ways to mix and react, making processes faster and more efficient.
Harnessing AI and Machine Learning
In the world of Process Intensification, AI and Machine Learning are like the brains behind the operation. They help in doing things smarter and faster.
Optimizing Processes and Detecting Faults
AI and Machine Learning work together to figure out the best ways to run chemical processes. These smart systems learn from data. They find patterns and suggest changes to make things better. It’s like having a personal assistant telling you the best moves to make!
But there’s more! These intelligent tools also help in detecting faults. If something is going wrong, they’ll spot it, fast. This is super important to avoid failures or accidents in plants. Thanks to this, we can ensure that everything is running just as it should. Dive deeper into how AI transformation impacts industries here.
These tools are the heroes behind making chemical processes lean and mean. And the story doesn’t end here. Armed with AI, we can continually strive towards an optimized future where errors are minimal, and efficiency is maximized. And that’s what makes chemical processes more thrilling than ever!
Future of Process Intensification
Let’s take a peek into the future of process intensification! Imagine a world where chemical plants are smarter, more sustainable, and super efficient. This is the dazzling future we are moving toward with process intensification. Now, let’s dive deeper into how digital integration and sustainable changes will play a role.
Digital Integration and Industry 4.0
Digital integration is not just a fancy term. It’s like giving a brain to our chemical processes. With Industry 4.0, everything becomes more connected. Computers and machines talk to each other. They share information and make everything work better. Imagine factories where everything is optimized in real-time.
Creating Self-Optimizing Plants
Self-optimizing plants are the future! Imagine a plant that thinks and fixes itself. With smart computers, sensors, and lots of data, these plants will learn how to run better all by themselves. They can adjust temperatures and pressures without human help. This means fewer mistakes, less waste, and more savings.
Note: These plants can automatically increase or decrease production based on demand. That way, they use less energy and materials.
Embracing Sustainable Changes
Sustainable changes mean making sure our planet stays healthy. In the future, process intensification will help chemical plants do this better. We will make smarter use of materials and reduce pollution.
Using Sustainable Feedstocks and Capturing Carbon
Plants will use sustainable feedstocks, which are materials that can be replaced naturally without hurting the environment. That’s like using sunlight or plants to make things instead of coal or oil.
Carbon capture is another exciting thing. This is when we grab the carbon dioxide from the air before it can harm the planet and put it somewhere safe or use it for making new products. It’s like giving carbon a new job!
Fun Fact: With carbon capture, we can even turn harmful gases into things like fuel or even new materials!
Learn more about sustainable feedstocks
Through digital integration and sustainable practices, process intensification is setting the stage for a smarter and greener future. We’re not just making processes better; we’re looking out for Earth, too!
One comment
Comments are closed.
[…] adoption of continuous flow processes is becoming a cornerstone for modern chemical manufacturing. In continuous flow systems, reactants enter and exit the system at a constant rate, allowing for […]