Revitalizing the Synthetic Fabric Industry: Polyester and Nylon Regeneration Towards a Circular Supply Chain
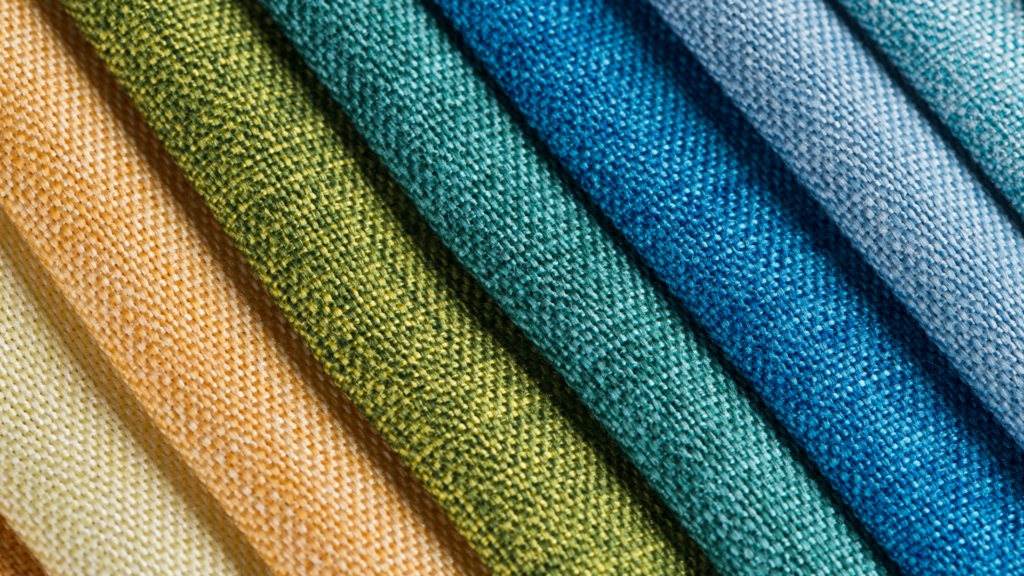
Ready to dive into the world of synthetic fabrics and dream a little dream of circularity? Today, most of our favourite tees and snazzy stretch pants owe their comfort and style to synthetic materials like polyester and nylon. Unfortunately, their production and disposal have a habit of making Mother Earth crinkle her nose. But wait! Imagine a future where these synthetic fabrics are born from a super cool, sustainable recycling process. Think closed-loop recycling, minimal environmental impact, and serious wardrobe envy without the guilt. Now, that’s a future worth striving for! From mind-bending technologies like glycolysis and PETase to the heartening success stories of Cycora® (Ambercycle), we’ll explore it all. So, buckle up! We’re about to journey through a whirlwind of innovation, collaboration, and the tantalizing opportunities of crafting a sustainable textile industry. This isn’t about a temporary fix. It’s about a resilient, beautifully circular future for synthetic fabrics – and we’re thrilled to have you on board!
Introduction to Synthetic Fabrics and Circularity
From the clothes we wear to the linens we use, synthetic fabrics like polyester and nylon certainly color our world. But what’s the real price we pay for these convenient, ever-present materials? Come with me on this incredible discovery journey!
The Role of Synthetics in Today’s World
In your house, your car, your office – the prevalence of synthetics is undeniable. They’re quick to make, easy to maintain, and they last longer than Forrest Gump’s run. Nylon is your stockings’ best friend, while your yoga pants can’t live without polyester. Some celebrate them as marvels of human invention, while others, well – they’re not so thrilled.
To put it simply, synthetics are everywhere! And therein lie the problem and the opportunity.
Environmental Impact and Waste Issues
Now, listen up because I ain’t gonna sugarcoat this. The environmental impact of synthetic fabrics is like a boomerang that just came back and hit us where it hurts. When you wash those nice, stretchy exercise pants, tiny bits called microplastics saunter their way into our waterways. Now, who in their right mind wants to gulp down plastics with their morning cup of joe? I know I don’t!
And then there’s a matter of waste. Picture this – every year, we dump enough synthetic clothing into landfills to almost reach the moon. Almost. That’s a heck of a lot of waste just sitting there, refusing to decompose.
Vision for a Sustainable Future
But let’s not be all doom and gloom here. There’s a vision, a glimmer of a greener future on the horizon. It’s called circularity, and it’s about as cool as it sounds. Imagine a world where your worn-out polyester shirt gets transformed into a new one. An endless circle of use, recycle, and reuse.
This closed-loop recycling or regeneration, as the smart alecks call it, can be our bargaining chip against resource depletion and environmental damage. It’s about time we start thinking in circles!
So, hold on to your seats and keep reading – we’re diving deep into this world of amazing possibilities. Because, after all, our future, much like fashion, is what we make of it! Let’s explore how we can dress up this world in sustainability, one thread at a time.
Understanding the Current State and Challenges
Let’s play detective for a bit. The first clue? A look at the synthetic fabric supply chain shows that it operates on a linear model.
The Linear Model and Its Drawbacks
What’s a linear model, you ask? Imagine a straight line. At one end, resources are taken from the ground. They’re turned into synthetic fabrics, like polyester and nylon. These fabrics are made into clothes, which are then bought and worn. And at the end of that line? The clothes are thrown away, ending up in landfills or incinerators. Pretty straightforward, right? Wrong. This “take-make-waste” model is a recipe for disaster. It depletes our resources, creates heaps of waste and doesn’t circle back to reuse what’s already available.
Resource Depletion and Pollution
Do you know it takes about 70 million barrels of oil to produce the polyester used in fabrics each year? And that’s just for polyester! The problem becomes even more alarming when we consider the pollution created in the process. Production of these fabrics releases harmful carbon emissions into the air. And when washed, these fabrics shed tiny plastic particles, called microplastics, that end up in our oceans. It’s like a trash-can nightmare.
Limitations of Current Recycling Methods
Now, you might wonder, “Why not just recycle?” Good question! Unfortunately, our current recycling methods are somewhat clunky. First, separating the different types of synthetic fabrics is a Herculean task. They’re often blended together, making it difficult to separate one fabric from another. Also, the process of recycling these fabrics often results in a lower-quality material, less suited for high-quality clothing. It’s like trying to turn a burger back into a cow.
Understanding these challenges is the first step. But don’t worry, it’s not all doom and gloom. Solutions that create circularity in the synthetic fabric supply chain are emerging, creating the potential for a system that’s simultaneously sustainable and economically viable. Stay tuned for the next part where we explore these promising breakthroughs!
Exploring Regeneration Technologies
We’re on a mission to push sustainability to the forefront, and the key lies in regeneration technologies. It’s like solving a complex puzzle, but don’t worry, I’ll help you get the picture. It involves some fancy chemistry and innovative ideas!
Chemical Processes: Glycolysis, Hydrolysis, and Methanolysis
First up, let’s talk about the chemical big guns: glycolysis, hydrolysis, and methanolysis. Mouthful, right? Let’s break it down.
Glycolysis (no, not the body process) in textile recycling refers to breaking down polyesters into their monomers using glycols. Often, this involves heating the material to high temperatures.
Then we’ve got hydrolysis, a process that uses water to split polyester into the monomer components. Requires a bit of heat too, but less than glycolysis.
And lastly, methanolysis. Similar to the other two, it breaks down the polyester into monomers using methanol. This process is friendly for large-scale industrial applications and is a popular choice.
Enzymatic Solutions: Cutinase, Lipase, and PETase
Moving on to something a bit more nature-friendly – enzymatic solutions. These make use of enzymes – little protein molecules that help speed up chemical reactions – to deconstruct synthetic fabrics.
We have cutinase, lipase, and PETase. Cutinase, for example, can break down polyesters, particularly PET plastic (that’s your soda bottles and food packaging) – without the intense heat needed for the chemical processes. Lipase also works in a similar way.
The new kid on the block, though, is PETase. This enzyme breaks down PET even faster than the others.
Emerging Techniques: Microwave and Supercritical Fluids
Just when you thought, “surely, that’s all the tech,” there’s more! We have microwave technology and supercritical fluids on the horizon.
Microwave technology uses, well, microwaves to heat and break down materials. Less energy, less cost – nice, right? But it’s not quite ready for the mainstream yet, so watch this space.
Then, there are Supercritical fluids (SCFs). When certain substances are exposed to both high pressure and temperature, they exhibit properties of both liquids and gases, becoming supercritical fluids. CO2 is often used, making this a greener choice.
Wow, that’s a lot of science, huh, but these are the puzzle pieces to a future of no landfill waste and sustainable clothing. We’re just getting started on this journey of creating circularity in synthetic fabric supply chains, but I’ve got a good feeling about it, and I hope you do too!
Polyester Regeneration Techniques
Let me walk you through the magic of turning old, used polyester into brand-new threads. It’s like a phoenix rising from the ashes! The process entails three main steps: Depolymerization, Purification, and Repolymerization. Let’s unpack these fancy terms.
Steps: Depolymerization, Purification, and Repolymerization
Depolymerization is our starting point. It’s when we break down the old, worn polyester into its building blocks, known as monomers. How? We use some super powerful chemicals or heat, to crack it down.
The second step is Purification. Remember, we are dealing with used stuff here. So, mixed in those monomers, we may find traces of dyes, finishes, or even tiny particles of dust or dirt. That’s where purification comes in. We need to thoroughly clean those monomers before they are fit for the next step.
The last step is Repolymerization. Here, we reconstruct our cleaned-up monomers back into polyester. We spin it, draw it, and voila, we have fresh, new polyester threads, ready for weaving or knitting.
Examining Successful Innovations: Cycora® (Ambercycle)
But alas! This isn’t all theory. Let’s take a real-world example. Heard of Cycora? It’s a commercial product by the folks at Ambercycle. What’s so special about Cycora you ask?
Well, my friends, Cycora is made from 100% recycled polyester. These people have taken our thrown-away textile and plastic bottle waste and transformed them into fresh, new polyester fabric!
Ambercycle’s approach is a fine example of embracing sustainable and circular practices in the production of synthetic fabrics. Their methodology not only provides an effective solution to manage textile byproducts but also ensures that the industry moves towards zero waste.
By following their footsteps, we can contribute towards a much needed closed-loop polyester regeneration. And who knows, your next tee might as well be made from the plastic bottle you dumped last week! Doesn’t that sound awesome?!
Stay tuned for more insights on making our fabric supply chains circular and sustainable!
Nylon Regeneration Challenges and Methods
When it comes to synthetic fabrics, creating a circular economy isn’t as simple as setting out a recycling bin. Let’s walk through some of the challenges and procedures involved in nylon regeneration.
Comparing Nylon 6 and 6,6
Two big players in the world of nylon are Nylon 6 and Nylon 6,6. Now, you might think that the difference between these two is minimal — it’s just a measly little comma, right? Wrong. That small punctuation marks a world of difference in their chemical structures, and that, my friend, means they require entirely different recycling processes.
Nylon 6 is the more “recycling-friendly” of the two. It’s a big fan of a process known as depolymerization. Nylon 6,6, on the other hand, throws a recycling wrench in the works because it’s much harder to depolymerize. Without a successful Nylon 6,6 depolymerization process available, recycling this type of nylon often involves downcycling, which means it’s turned into a product of lesser value. We’re shooting for closed-loop recycling here, so that’s not ideal.
Understanding Depolymerization Methods
Depolymerization — yeah, it’s a bit of a mouthful. But here’s what you need to know: Depolymerization breaks down a material (like Nylon 6) into its original constituents in a process that is essentially reverse polymerization.
For Nylon 6, the standard depolymerization process relies on the use of heat and pressure. In simple terms, we cook the nylon and pressurize it until it falls apart into caprolactam, the building block of Nylon 6. This caprolactam can then be cleaned up and reused to make new nylon, completing the recycling loop.
Specific Recycling Challenges for Nylon
Even with depolymerization, recycling nylon isn’t a walk in the park. One of the biggest obstacles? Contamination. Nylon often gets “dirty” with dyes, additives, or other materials that contaminate the caprolactam during depolymerization. The contaminated caprolactam can’t be used to make new nylon, which puts a damper on our recycling efforts.
Another biggie in the challenge department is the collection process. Since only specific types of nylon can be recycled, the potential exists for those non-recyclable nylons sneaking into our recycling stream, causing contamination or, worse, ruining a batch of caprolactam.
We also need to gird ourselves for scalability issues. Depolymerization might sound great in theory, but can we scale it up to handle the massive amounts of nylon waste generated every year? And do this without a bulging price tag? It’s a question we must consider.
Sure, the world of nylon regeneration holds some thorny challenges, but don’t count us out — we’re forging ahead, creating solutions, and innovating towards a closed-loop system. With a touch of grit and some smart science, our synthetic fabric future is looking bright.
Designing Products for Circularity
Designing products with a circular perspective is an essential step towards creating a sustainable fabric supply chain. This process, from the beginning, envisages end-of-life scenarios, encourages the selection of materials that are resilient yet easy to recycle, and considers the potential ‘break points’ in polymers that may facilitate their recycle process.
Identifying ‘Break Points’ in Polymers
The concept of ‘break points’, in a polymer context, refers to the part in a polymer’s structure where it is prone to breaking or splitting. These points are mainly the chemical bonds holding the units of a polymer together. Locating these break points and understanding their nature is crucial in designing for circularity.
Cutting these polymers at the break points allows them to be effectively deconstructed during recycling, and then reconstructed into new fibers. This method allows us to keep materials at their highest value and utility at all times, minimizing waste.
Balancing Durability and Recyclability
A key challenge in designing for circularity in synthetic fabrics is striking a balance between durability and recyclability. We want our clothes to last, but we also need them to break down easily when it’s time to recycle them.
The ideal scenario is to engineer fabrics that are tough enough to stand up against wear and tear but are also designed in a way that they can be readily recycled—ideally, again and again, in a closed-loop system. Remarkable strides are being made in this direction, with innovative materials and design techniques emerging that are both robust and recyclable.
Design Considerations for End-of-Life
When designing for circularity, considering the end-of-life scenario for a product is crucial. It’s simple – if a product is hard to recycle, it likely won’t be. Factors like mixed materials can make recycling challenging. A common example is a shirt made from a blend of cotton and polyester – right now, it’s difficult to separate the two materials, and it often ends up in the landfill.
By considering the end-of-life in the design stage, we can create products that are easier to recycle and will have a significantly better chance of being turned into something new rather than going to waste.
In conclusion, each of these design considerations plays a key part in moving towards a more circular economy in synthetic fabrics – a challenge that is undeniably complex, but equally vital. We’re just at the beginning of this journey, but with effort and innovation, a future with closed-loop synthetic fabric regeneration is within our grasp.
Building a Circular Supply Chain
Think of it as a relay race. You’re talking about a baton that needs to get handed off smoothly to each person to get it around the track as fast as possible. The same concept applies when we’re developing a circular supply chain in synthetic fibre recycling. It involves a series of handoffs: each step carefully coordinated with the next one to keep the whole operation humming along.
Effective Collection and Sorting
The relay race begins with effective collection and sorting. Imagine your closet filled with clothes – some are pure polyester, some are pure nylon, and others are blends. But how do you separate them? To make recycling work, we need to start with efficient sorting methods. Many companies today are developing next-generation technologies to tackle this issue. From infrared scanners to automated sorting systems, technology is helping us distinguish between different types of fabric swiftly and accurately. This step is critical in creating the perfect ground for our recycling race.
Ensuring Traceability with Technology
Second in line, we have traceability over our baton. Now, we’ve got big heaps of sorted synthetic fabrics, but where did they come from? That’s where technology like digital tags and blockchain come in. These tools create a tech-powered breadcrumb trail that tells the story of each garment, from the first stitch to the recycling bin. Knowing the history helps us make smarter decisions about how to recycle each item and bring trust and transparency to our circular supply chain.
Fostering Collaboration Across Stakeholders
Finally, we can’t forget the importance of team spirit. Like a relay, where teamwork determines the outcome of the race, building a circular supply chain is not the job of a single entity but a collection of stakeholders. Textile manufacturers, fashion brands, recyclers, governments, and consumers, everyone has a role to play. By fostering collaboration and establishing shared goals, we can amplify our efforts and make a greater collective impact towards a more sustainable fabric industry.
In essence, building a circular supply chain is quite the relay race, where sorting gives us our starter’s gun, traceability sets the pace, and collaboration brings us over the finish line. Together, we can build a synthetic fabric supply chain that does more than just make clothes – it protects our Earth. And that’s a race we all want to win.
Overcoming Recycling Challenges
Picture this. You’ve just finished a refreshing soda, and you’re holding the empty plastic bottle in your hands. Now, what do you do with it? That’s right – you recycle it. Well, folks, when it comes to synthetic fabrics, the stakes are just as high, and the challenges? Even bigger.
But here’s the good news: With the right strategies and technological advancements, we can tackle these challenges head-on. So, let’s dive right in!
Handling Mixed Waste and Removing Dyes
Now, one of the biggest hurdles in recycling synthetic fabrics lies in sorting and treating mixed waste. This is like taking a box of jigsaw puzzle pieces from several puzzles jumbled together, and trying to separate the pieces belonging to each individual puzzle. Not such a piece of cake now, is it?
Moreover, lots of synthetic fabrics are dyed in some fantastic colors that make our clothes look fabulous. But when it comes to recycling, these dyes present a huge challenge. The recycling process needs to get rid of these dyes so that the recycled fabric can be re-dyed to the desired color.
Thankfully, innovative solutions are popping up! Cutting-edge technologies enable us to sort mixed waste with high accuracy. As for those stubborn dyes, scientists have developed some great new ways to remove them without harming the quality of the recycled yarn. These sound like some mighty fine reasons to be optimistic, don’t you think?
Maintaining Fiber Quality and Scaling Up
Next on our challenge hit-list, we have the issue of maintaining the quality of the regenerated fibers. Here’s the deal: When synthetic fibers are recycled, there’s a risk that the quality of the fabric might take a hit. Nobody wants to wear clothes that feel like sandpaper, right? Well, advanced recycling technologies are here to save the day (and the feel of our comfy clothes). These nifty techs can regenerate fibers that are as good as new!
Another elephant in the room is scaling up the recycling process. Think about it – we need to recycle a whole lot of synthetic fabric if we’re serious about making a dent in the waste problem. But scaling up also means maintaining consistent quality, and that’s not always easy. The key here lies in developing robust and efficient recycling systems that can handle large volumes without compromising on the quality.
So there you have it, folks! Sure, the path to recycling synthetic fabrics is fraught with challenges. But remember, it’s within these problems that we sometimes find the greatest opportunities. By finding innovative ways to handle mixed waste, remove dyes, maintain fiber quality, and scale up the process, we can make some real progress towards a sustainable and stylish future! How about that?
Policy and Regulation in Textile Recycling
Let’s level with each other, folks. The game of textile recycling isn’t just about the fancy new technologies or the green ideas. No sir! It also involves a whole lot of rule-making and rule-following. That’s right, ladies and gentlemen: we’re getting into the nitty-gritty of policy and regulation.
Extended Producer Responsibility (EPR)
Let me introduce you to a dear friend of mine: Extended Producer Responsibility (EPR). EPR is like that friend who reminds you to clean up after your birthday party. Essentially, it’s a policy approach that puts the responsibility of recycling and disposing of products right back on the companies who created ’em.
But EPR isn’t just about pointing fingers and saying, “Hey, you made this mess, you clean it up!” It’s also about encouraging these big producer folks to design products that are easier to recycle in the first place.
Even more, EPR can reshape the textile industry by making every step of a product’s life cycle—from design to disposal—more circular. With EPR, producers might feel some heat to reduce material use, select more sustainable materials, and create products that last longer. And less waste ain’t just good for the planet—it’s good for business, too!
Incentives and Standardization
Now, on to the next big player in the policy and regulation game: Incentives and Standardization. We’ve all been there. A lil’ nudge or treat can go a long way in encouraging us to do something. Same goes for recycling. Incentives can push businesses and consumers to take part in the recycling movement and make the eco-friendlier choice.
Tax breaks, grants, subsidies—you name it—these incentives can help soften the financial blow companies might face when shifting toward circular models for their synthetic textiles.
And let’s not forget about standardization. Picture this folks. You’re making a cake – but every recipe you find is using different measurements. One says grams, one says ounces, and one even says cups. Frustrating, right? That’s why we need standardization. Textile recycling can be all over the place without some standard guidelines.
Standardization makes sure everyone’s playing by the same rules, whether it’s the way recycled products are labeled, or how the recycled content is calculated.
In the end, policy and regulation in textile recycling are about creating the groundwork for a more circular and sustainable industry. From EPR to incentives and standardization, they are the unseen heroes in our battle for circularity in synthetic fabric supply chains!
Engaging Consumers and Education
The real power lies in the hands of consumers. They have the ability to reshape the future of synthetic fabric, and that’s exactly where we need to start.
Raising Awareness About Recycling
Not everyone knows about the true threats of synthetic waste. Plastic bottles? Sure, those are bad. But synthetic fabrics? Many wouldn’t have a clue. So, one of the first ways we can improve our environmental impact is by raising awareness about recycling. That means spreading the word about the importance of recycling your clothes, making people aware of recycling facilities, and showing them just how easy it is to be a part of the solution.
Promoting Proper Disposal Practices
Education isn’t just about making people aware, though— we need to show them how to do it, too. This is where promoting proper disposal practices comes into play. Many people want to do the right thing; they’re just not sure how. We can guide them by providing clear instructions, making recycling bins more available, and ultimately making it easy to do the right thing. Show folks that recycling that old polyester shirt isn’t an impossible task!
Understanding the Value of Recycled Textiles
Finally, we need to help everyone understand the value of recycled textiles. It’s not just ‘waste’—it’s a resource! When you recycle an old garment, you are playing a powerful part in reducing the use of virgin materials, decreasing overall waste generation, and contributing to a more sustainable future.
Creating circularity in synthetic fabric supply chain is no small task, but with shared effort and understanding, we can transform our environments, our industries, and our world. Let’s promote this power of transformation!
Exploring Economic Opportunities
In our quest for sustainability in synthetic fabric supply chains, there’s a cornucopia of untapped economic potential just waiting to be explored. And it’s not just about being nice to Mother Nature, folks. What we’re talking about here can create jobs, reduce dependence on original resources, and pave the way for groundbreaking business models. Let’s dive right in.
Creating Jobs Through Recycling Initiatives
Imagine this: instead of chucking out your old, worn-out polyester and nylon clothes, you take them to a local recycling center. Workers sort through the fabric waste, separating out reusable fibers. Specialists use high-tech machinery to regenerate those fibers, creating new raw material for the textile industry. Sounds like a lot of work, right? It sure is! That’s why recycling initiatives are such a fantastic source of job creation.
From collection and sorting, to processing and sales, every step of the recycling journey has the potential for employment. With the right training, even people without formal qualifications can find meaningful work in this sector. We’re talkin’ jobs that help the planet and put money in people’s pockets. Now, that’s what you call a win-win!
Reducing Material Dependence
Ever wonder just how much crude oil goes into making nylon and polyester? Answer: A whole freakin’ lot! In fact, some 70 million barrels of oil are pumped out of the ground each year just to satisfy the world’s lust for synthetic fabrics. But get this: By switching to a closed-loop recycling system, we could significantly slash our reliance on this non-renewable resource.
Material dependence isn’t just a drain on the environment. It also puts companies at the mercy of fluctuating commodity prices, and that’s just bad for business. But with recycled raw materials, supply becomes much more predictable and under our control.
Innovative Business Models
Now listen up, entrepreneurs. If you think eco-friendliness and profit can’t go hand in hand, think again! Creating circularity in synthetic fabric supply chains opens up exciting new opportunities for business innovation.
We’re not just talkin’ textile producers and fashion retailers, here. Every part of the supply chain, from logistics providers to recycling technology developers, has room to grow. Already we’re seeing pioneers like Ambercycle making a splash with their Cycora® polyester, made from recycled beverage bottles. And trust me folks, it’s just the tip of the iceberg!
So, whether you’re an aspiring entrepreneur, a concerned consumer, or just someone who’s keen on creating a sustainable future, the economic opportunities in synthetic fabric recycling are well worth exploring. Let’s roll up our sleeves and get to work, shall we? We’ve got a planet to save!
Future Outlook and Emerging Trends
The future of synthetic materials looks promising, my friends. Not in a way that would damage our beloved planet further, but in a way that corresponds to its well-being. So, let’s delve in to understand the road ahead.
Advancements in Other Synthetics
In terms of advancements in other synthetics, consider this: Day by day, we are witnessing a plethora of developments. Modern innovators have their eyes and minds set on finding alternatives for traditional synthetic fabrics, aiming to improve efficiency and reduce harm. We now have better versions of acrylic, rayon, and spandex – each redesigned to be more planet friendly.
Look out for these smarter synthetics! As time unfolds, we are sure to see more cutting-edge developments on the horizon, ensuring sustainability in a glossy, fashionable guise.
Bio-based and Recycled Blends
The conversation gets even more interesting when we talk about bio-based and recycled blends. Enter: the blending of natural and synthetic fibers.
Industries are now exploring options to mix natural bio-based fibers like cotton, hemp, and bamboo with regenerated synthetics. Sounds interesting, doesn’t it? It’s a powerful duo. It’s like adding vegetables to your favorite meaty burger; you amp up the nutritional value without compromising the taste!
This novel approach provides textiles with the best of both worlds. Besides being durable and comfortable, these blends are also designed to be easier to recycle, making fashion circular.
Exploring Biodegradable Synthetics
Lastly, let’s peek into the world of biodegradable synthetics. A step beyond recycling, the goal here is to develop synthetic fibers that would not just be recyclable, but also biodegradable.
Imagine this: Your favorite synthetic fabric that serves you for years, then, at the end of its life cycle, quietly returns to the earth without leaving any damaging traces behind.
That’s a complete circular economy, ladies and gentlemen! We are not quite there yet, but remember, Rome was not built in a day!
Folks, the future of the textile industry is all about blending nature with science, without harming Mother Earth. The challenge is complex, but we are steadily progressing to a future where synthetic fabric supply chains are circular and sustainable.
It’s a beautiful vision worth striving for. So, let’s embrace it and champion it, showing our planet the respect it deserves!
Measuring Success in Circularity
Success, they say, is when preparation meets opportunity. But in the realm of circularity with synthetic fabrics, success lies in numbers—numbers that show progress, change, and sustainability.
Tracking Recycled Content Usage
Success starts with the question: How much are we really using recycled content? The answer lies in careful tracking systems. In the world of textiles, that means barcode technology tagging every fiber and cloth. This way, we know exactly how much recycled polyester or nylon is being used in our jeans, our jackets, our jumpers. And folks, more use of recycled content means less reliance on virgin materials. It’s the first step to a greener, cleaner, circular textile industry.
Reducing Virgin Material Use
Next on the scorecard is reducing virgin material use. This is where we talk tough and make hard-hitting decisions. Every strand of virgin polyester or nylon counts. Imagine this – in the time it took you to read this paragraph, thousands of clothes have been made worldwide using new, raw materials. We aim to reduce this—we aim to replace virgin with recycled. It may seem like rocks up a hill, but every step will surely make a significant difference!
Decreasing Overall Waste Generation
And finally, we come upon one of the most undeniably important measures: waste. Yep, you heard it—waste. The less waste we make, the better. So we need to keep our eyes on the waste generation. From production to the disposal of our beloved garments, every stage matters. We aim for not just less waste, but the least. Every bit of material saved from landfill is a success in our books.
In a nutshell, to measure success in circularity for synthetic fabrics, we follow the three “R”s: Record (Track use of recycled content), Reduce (lower virgin material use), and Restrict (minimize waste generation). Remember, every step forward is a stride towards a sustainable, circular textile industry. Now that’s what I call success worth cheering for!