Powering Circularity for Battery Metal Recovery and Sustainable Extraction
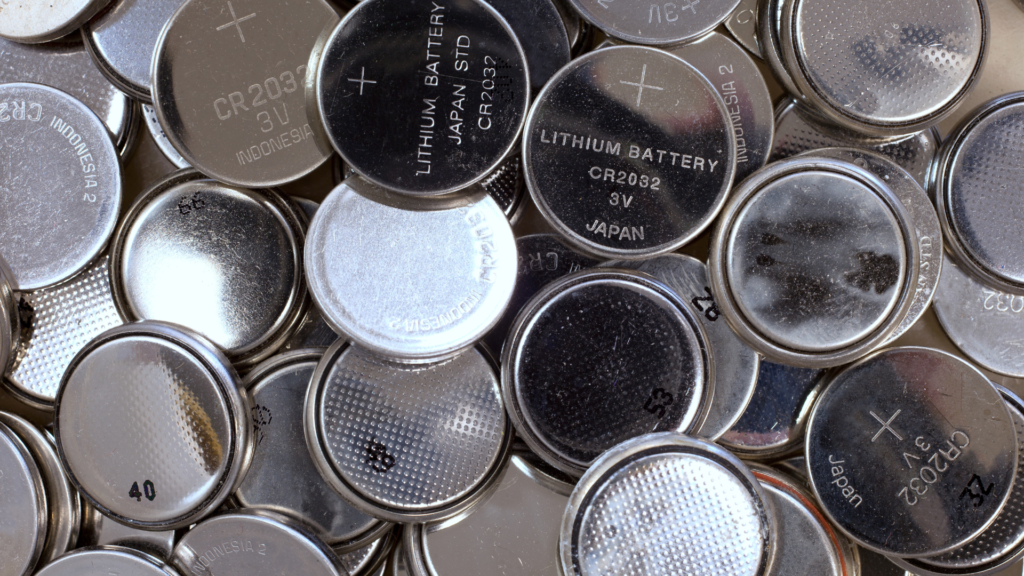
Welcome to the grand world of circularity in the battery metal recovery supply chain, where we spark new life into old batteries, unlocking the potential of valuable metals like lithium, cobalt, and nickel. These tiny sparks of energy, despite their incredible worth, pose a significant challenge in our supply chains, with a myriad of technical, economic, and regulatory hurdles to overcome. However, don’t fret, for every challenge we see an opportunity. From enhancing extraction through advanced hydrometallurgy and direct recycling to innovative circular business models, we strive to maximize recovery and minimize our dependency on mining. Set sail with us on this exciting journey towards a more sustainable, greener, and innovative future, where every step forward is a leap towards achieving resource efficiency, economic growth, and environmental preservation.
Circularity’s Role in Battery Metal Recovery
Creating circularity in battery metal recovery isn’t just a nice-to-have. It’s a must! As we become more dependent on batteries, particularly lithium-ion ones, we’re faced with a new challenge. What do we do with the metals inside once these batteries become obsolete? Lithium, cobalt, and nickel are the heart and soul of these power packs, and their destiny is in our hands.
The Significance of Lithium, Cobalt, and Nickel
Without Lithium, cobalt, and nickel, batteries would be like a car without gas. These metals are critical elements in battery production. Lithium’s lightness and ability to store high-energy capacity make it the keystone for rechargeable batteries. Then there’s cobalt, which stabilizes and maximizes the efficient use of lithium. Meanwhile, nickel helps increase the energy density and storage capacity.
Yet, these batteries don’t grow on trees. Lithium, cobalt, and nickel are mined from the earth, in processes that strain our environment and are burdened with a limited supply. However, they can be found in abundance in the used batteries that we discard each year. To ensure their use for future generations, we have to get them back into the production cycle, minimize waste, and reduce dependency on mining. That’s where ‘circularity’ comes in!
Challenges in Metal Supply
Not everything is smooth sailing, though. Scarcity of these metals, combined with heavy demand and geopolitical constraints, makes sourcing a high-wire act. Mining brings its share of environmental issues, from land degradation to water pollution. It’s a tough balancing act, but the circular economy approach promises a positive outcome.
We’re now looking at not just ‘take, make, dispose’, but a loop where we ‘recover and regenerate’. We’re replacing ‘end of life’ with an endless life for these metals. But to make this vision a reality, we must overcome numerous challenges in technical, economic, and regulatory realms.
In our next section, we’ll delve into these challenges and explore how improved extraction methods can address them. Stay with us on this journey into the future of battery recycling.
Complexities in Recovery Processes
When we talk about creating a circular economy in the arena of battery metal recovery, we can’t overlook some of the momentous challenges we face. So, let’s plunge right into them.
Technical Obstacles: Battery Chemistry
First, let’s tackle the technical behemoth in the room – the complex, intricate chemistry of batteries. Different members of the battery family, such as lithium-ion, nickel-cadmium, or nickel-metal hydride, each have a unique internal structure and chemistry.
To make things even trickier, each model of lithium-ion battery can have different cathodes made of either lithium manganese oxide, lithium cobalt oxide, lithium nickel manganese cobalt oxide, or lithium iron phosphate. This diverse chemistry means that there’s no single one-size-fits-all solution for the recovery of these metals.
The mixture of metals in batteries makes it hard to separate and extract the individual metals effectively. On top of that, the compact design of batteries, crafted to maximize energy density, can make disassembly and metal extraction a tough gig.
Economic Barriers: Costs and Market Changes
Next, we square off with the elephant in the room – the economics of battery recycling. Here’s the raw truth: recycling batteries can be expensive. It involves high-cost processes such as manual disassembly, hazardous waste handling, and advanced chemical treatment.
Market volatility can also put a crimp in things. Battery metal pricing fluctuates like a roller coaster, influenced by changes in supply and demand. If the prices drop, the economic viability of recycling also drops, making it a risky financial investment for businesses to venture into.
Regulatory Difficulties: Policies and EPR
And finally, we confront the labyrinth of regulatory difficulties. Inconsistent and disjointed global policies around battery disposal and recycling can frustrate the push for circularity. For example, rules about transport and disposal of batteries vary from country to country, creating substantial complications in creating a coordinated, global recycling effort.
Moreover, the lack of Extended Producer Responsibility (EPR) regulations in some parts of the world can hinder the development of recycling programs. EPR laws are designed to shift the waste disposal responsibility from governments to the manufacturers creating the product. Without these laws, manufacturers lack the incentive to design batteries that are more recyclable and easier to handle at the end of their lifespan.
In a nutshell, transforming the metal recovery process into a well-rounded circular system doesn’t happen overnight. It’s a process riddled with complexities from the microscopic battery chemistry to global market trends. That being said, it’s also a surefire opportunity for innovation, improvement, and evolution. After all, overcoming challenges is what drives progress, isn’t it?
Methods to Boost Metal Extraction
When it comes to breathing new life into used batteries, the science can get a wee-bit complicated. But don’t you worry your pretty little head about it – we’re here to break it down for you! The goal is simple: enhance the extraction of precious metals like lithium, cobalt, and nickel. Let’s dive in.
Pre-treatment Strategies
To kick things off, we need to get these batteries ready for the main event. This is where pre-treatment comes into play.
Automated Disassembly
Imagine trying to pull apart hundreds of batteries a day, by hand. Talk about a nightmare! That’s why folks much cleverer than me developed automated disassembly. These nifty machines break down batteries into smaller pieces, making it easier to get at the good stuff inside.
AI-Assisted Sorting
I know what you’re thinking – what doesn’t AI do these days? You’re right – it’s even helping sort out battery components! AI-assisted sorting distinguishes between different materials, ensuring each part ends up in the right place.
Hydrometallurgy Techniques
Once the batteries are all broken down and sorted, it’s time for the real magic – extraction.
Eco-Friendly Leaching
Good news for all you nature lovers out there – some fantastic eggheads invented eco-friendly leaching. This process uses safe, environmentally friendly chemicals to dissolve the metals we’re after, making it easier to extract them.
Direct Lithium Recovery
Want to know a secret? Lithium’s a bit of a superstar in battery production, but it isn’t the easiest fella to extract. That’s where direct lithium recovery comes in. It’s a fancy way of saying, “We’ve got a faster, cleaner method to get lithium out of used batteries.”
Pyrometallurgy Innovations
The final piece of the puzzle is pyrometallurgy. Try saying that ten times fast, eh?
High-Temperature Smelting
Fire and heat can be more than just a barbeque’s best friend. High-temperature smelting uses the power of extreme heat to melt battery components, making it easier to separate and recover the metals.
Slag Reduction
During smelting, a waste product called slag is created, and we want to reduce it as much as possible. Because, let’s be honest, who wants more waste? Various techniques are used to cut back slag and make the whole process more efficient.
There you have it, folks! Isn’t science fun? Enhancing metal extraction is an essential step to creating a circular battery supply chain. It helps us get more bang for our buck and makes the planet a happier place to boot. Stick around as we dive deeper into making battery circulation a reality.
Establishing Circular Business Models
In the world of battery metal recovery, establishing circular business models is the new buzz phrase. These models aren’t just trendy; they’re instrumental to maximizing metal recovery and reducing our dependency on mining. Let’s dive into some key strategies.
Implementing Take-Back Programs
Coming up first, the implementation of take-back programs. Isn’t it a pain when you have old batteries lying around but you’re not sure how to safely dispose of them? This is where take-back programs come in. Companies offer their customers an easy and environment-friendly way to return their used batteries. The returned batteries then get a chance to enjoy a ‘second life’ through recycling or repurposing. How cool is that?
Developing Reverse Logistics
However, taking back batteries is just the first step. To get our metals back, we also need to focus on developing reverse logistics. This is like a delivery service in reverse, where products travel from the customer back to the manufacturer. For example, by setting up collection points and arranging shipments, used batteries can get to where they need to be for recycling. It sounds complicated, but with a solid plan, reverse logistics can keep valuable metals in the loop and out of our lands.
Exploring Second-Life Applications
Our next strategy is exploring second-life applications for our batteries. Believe it or not, a battery’s life doesn’t have to end when it can no longer power your device. By giving them a second life through repurposing, they can continue to be useful in applications like energy storage systems. Can you already feel the immense potential?
Encouraging Value Chain Collaboration
Last, but certainly not least, we need value chain collaboration. This means everyone involved in a product’s lifecycle needs to work together. From the companies who mine our metals, to those who make the batteries, to those who recycle them, and, of course, the end-user. When we all work together, we create a true circular economy: saving resources, creating jobs, and helping our environment.
In summary, by establishing these key elements of circular business models, we can make sure our precious metals keep on giving, without needing to dig up more of Planet Earth. Now isn’t that something to strive for?
Forecasting Future Trends
As we stand at the brink of a fresh start, it’s vital to extend our gaze into the days ahead. In uncharted territories, forecasting future trends becomes a crucial survival skill for businesses and communities. The world of battery metal recovery is undergoing rapid change, so let’s dive deep into our future!
Innovations in Bioleaching
Bioleaching is like the tauntingly elusive gold nugget in the rough stream – full of potential and worth the hard pursuit. Bioleaching uses friendly microscopic bugs to tease precious metals like lithium, cobalt, and nickel out of scrap batteries. The exciting part? These tiny helpers consume less energy and inflict lesser damage on our environment. Less mining, more munching. We foresee an impressive leap in bioleaching techniques, which could spur the drive towards sustainable metal recovery.
Optimization with AI Technology
Next, let’s talk about artificial intelligence. The trusty steed of the digital age, AI technology, is ready to get its feet dirty (or circuits, technically) in metal recovery. Future trends point towards AI-driven optimization with superior sorting, precision separation, and intelligent forecasting abilities. With AI, we can reduce erroneous manual handling, lower energy consumption, and boost yield. Think of AI as your personal dairy cow – nurtured properly; it yields a steady stream of high-quality milk (or reclaimed metals, in our case).
Advancing Sustainable Battery Chemistries
Peeking further into the crystal ball, we see a future brimming with myriad sustainable battery chemistries. Imagine batteries that last longer, perform better, and have a lesser impact on our planet. Future batteries may well ditch unfriendly elements like cobalt, in favor of more environment-friendly alternatives. As battery makers and recyclers band together in this exploration, it might just usher in a new era of ‘green’ energy storage.
The future of battery metal recovery is an exciting frontier. Embarking on this journey, we may encounter surprising twists, unexpected milestones, and daunting challenges. Yet, with persistent innovation and strategic forward-thinking, we’re unlocking new pathways to a more sustainable world. After all, as the sage of the copywriting world, Gary Halbert, once said, “What you need to know about the next ten years… you can learn in the next ten minutes.” So, let’s strap in and ride into our intriguing future!
Examining Current Practices and New Innovations
In the exciting world of battery metal recovery, we’ve seen some mind-boggling technologies and bold practices which are as handy as a Swiss Army Knife. Let’s do a deep dive to explore what’s percolating under the surface.
Traditional and Advanced Methods
Starting with the bread-and-butter of this industry, traditional methods of recovery have provided a sturdy foundation. These methods, including hydro, pyro, and direct, have drawn out lithium, cobalt, and nickel from old batteries, much like pulling a rabbit out of a hat.
However, they also come with limitations. Picture yourself trying to run in a marathon with very tight shoes – that’s exactly how these traditional methods feel in this dynamic industry.
Cobalt extraction, for instance, faces the pressure of maintaining high recovery rates while ensuring eco-friendly processes. It’s akin to a juggling act in a circus, balancing raw material consumption, cost, and environmental impacts.
Enter advanced methods. They’re the answering bell to the shortcomings of traditional methods. For example, advanced hydrometallurgy makes use of eco-friendly leaching, producing less waste than pyro methods. It’s a bit like switching from using a paper map to a GPS; it’s more efficient, eco-friendly and saves you valuable time.
Biohydrometallurgy is another groundbreaking method which uses microorganisms to leach metals out of minerals, as effortlessly as slicing through a birthday cake.
Lastly, green solvents like ionic liquids are leading the way in providing environmentally-friendly solutions, much like switching incandescent light bulbs to LED ones.
Emerging Technologies and Success Stories
Now, let’s put the spotlight on the remarkable tales of triumph and innovation in our industry. Amidst all of these game-changing techniques, AI-driven optimization has made quite a stir. It’s akin to having a trusty sidekick with superpowers, helping sort and classify batteries for effective recovery.
Bioleaching is another emerging technology that promises to repackage waste into value. It’s a twist that would even surprise Alfred Hitchcock, turning the ‘trash’ in waste batteries into a ‘treasure’ of valuable metals.
Success stories? Get the popcorn ready! There’s plenty to celebrate. For instance, we have companies harnessing the power of direct lithium recovery techniques to produce battery-grade lithium in less time than it takes to watch a movie.
There are companies that have successfully integrated blockchain tracking with their supply chain to ensure traceability of recycled batteries, effectively turning a maze into a breezy walk in the park.
In all, these current practices and innovations are a testament to mankind’s ingenuity and persistence in the face of various challenges. They are engineering marvels, adding value where there was none, and saving our precious planet in the process. It’s not rocket science, it’s battery metal recovery!
So buckle up, for the journey of battery metal recovery is filled with innovation and stories that are just waiting to be told. The future beckons promisingly, and believe me, we’re all set to rock and roll!
Designing Batteries for Recycling
As we delve deeper into the world of renewable energy and clean tech, the role of battery design has never been more critical.
Focusing on Battery Design and Standardization
A crucial cornerstone is to craft batteries with recycling in mind from the get-go. The recognition is growing that we shouldn’t just think about a product’s life in terms of use but also consider what happens when it reaches the end of its useful cycle.
With lithium, cobalt, and nickel, we’ve got potent metals that are too valuable and environmentally harmful to simply discard. But to reclaim these elements efficiently, we need a clever design.
Standardization is one approach worth examining. By creating batteries that share a common design, we cut the clutter and make the recycling process simpler and more cost-effective. We get rid of the guesswork, deal less with the unknown, and face fewer surprises. Imagine a world where your local recycling center can handle your old batteries with the same ease as they deal with your cardboard and can recycling!
The key is standardization, reducing the variety of components to make disassembly and metal recovery less of a puzzle and more of a streamlined process, more akin to an assembly line in reverse.
Creating Strong Policy Frameworks
Yet, smart design is just half of the equation. We also need robust policy frameworks supporting these recycling efforts. It’s one thing to make something recyclable. It’s another to ensure it gets recycled.
Bring on extended producer responsibility (EPR). Under EPR schemes, battery producers get incentivized or legally mandated, or both, to take responsibility for their products’ end-of-life. It’s about ensuring that those who design and sell batteries also have a hand in recycling their products. EPR helps close the loop, nudge circularity along, and ensures everyone has skin in the game when it comes to recycling batteries.
Creating a successful policy framework also means thinking beyond national borders. Metal supply chains are global, and so too must be our efforts to recycle. Striving for international collaborations and shared incentives can get us closer to a world where every battery gets a second chance.
We should also invest in awareness campaigns about how and why to recycle batteries. The average user needs to join us in our recycling journey and be part of the solution.
When it comes to designing batteries for recycling, we’re not talking about a single knockout punch to the challenge but a series of jabs – good design, strong policies, and engaged consumers. The aim? A circular economy where every battery finds its way back into the system, and valuable metals are never lost to landfill.
Stay tuned as we delve into the economic and environmental benefits of battery recycling and how we aim to shape the future.
The Benefits and Future Directions
Aiming to maximize the recovery of precious metals like lithium, cobalt, and nickel from used batteries, we don’t just contribute to environmental conservation but also stand to gain economically. And our quest to innovate doesn’t stop here. Emerging technologies are continually being tracked, ensuring that we don’t miss out on any potential improvements in our processes!
Economic Gains and Job Creation
Creating circularity in the battery metal recovery supply chain holds immense financial benefits. As we recycle more, our dependency on mining reduces, curtailing costs and risks associated with extracting from the earth. Moreover, recycling holds the potential for job creation, offering positions in collection, disassembly, sorting, and more. It’s like finding the proverbial pot of gold at the end of the rainbow, except this time it’s lithium, cobalt, and nickel that we’re after!
Environmental Conservation Efforts
As exciting as the financial benefits are, the environmental conservation resulting from our efforts is the real star of the show. Every ounce of lithium, cobalt, or nickel that we recover from used batteries is an ounce we don’t need to mine. It equates to less earth being disturbed, fewer habitats being destroyed, and less water being contaminated. By enhancing the extraction of battery metals, we contribute significantly to preserving our valuable ecosystems.
Tracking Emerging Technologies
As active seekers of innovation, we keep a keen eye on technological advances to improve our operations. Whether it’s AI-driven automation for sorting or bioleaching techniques for an eco-friendlier recovery, no stone goes unturned. As novel technologies emerge, they hold the potential to redefine the way we extract metals from used batteries, making our process more efficient, cost-effective, and eco-friendly. By keeping abreast of these advancements, we ensure that we ride the wave of innovation, rather than getting left behind.
In summary, enhancing lithium, cobalt, and nickel extraction from used batteries through circularity leads to substantial economic gains, job creation, reduced environmental impact, and the successful harnessing of emerging technologies. It’s clear that the future of battery metal recovery is not just bright—it’s positively electrifying!